Техническое обслуживание и ремонт тормозных систем К основным неисправностям тормозной системы относятся: неэффективное действие тормозов, заедание тормозных колодок, неравномерное действие тормозных механизмов, плохое растормаживание, утечка тормозной жидкости и попадание воздуха в систему гидравлического привода, снижение давления в системе пневматического привода, а также негерметичность системы пневматического тормозного привода. . Неэффективное действие тормозной системы является результатом загрязнения или замасливания тормозных колодок, нарушения регулировки тормозного привода и тормозных механизмов, попадания воздуха в систему привода, уменьшения объема тормозной жидкости, негерметичности в соединениях гидравлического или пневматического привода. Заедание тормозных механизмов может произойти в результате следующих причин: поломки стяжных пружин, обрыва заклепок фрикционных накладок, а также в результате засорения компенсационного отверстия в главном тормозном цилиндре или заклинивания поршней в колесных тормозных цилиндрах. Неравномерное действие тормозных механизмов может привести к заносу автомобиля или к его уводу в сторону. Неравномерное торможение является следствием неправильной регулировки тормозных механизмов. Попадание воздуха в систему гидравлического привода снижает эффективность тормозной системы. Для нормального торможения в этом случае необходимо делать несколько нажатий на педаль. При утечке жидкости происходит полный отказ всей системы торможения автомобиля или какого-то отдельного контура. При ежедневном техническом обслуживании автомобиля необходимо проверять работу тормозов в начале движения, а также герметичность соединений в трубопроводах и узлах гидропровода и пневмопривода. Утечку тормозной жидкости из системы торможения контролируют по подтекам в местах соединений, а также по уровню жидкости в бачках. Утечку воздуха определяют по снижению давления на манометре или на слух. Утечку воздуха определяют при неработающем двигателе. В процессе первого технического обслуживания выполняют работы, предусмотренные ежедневным осмотром, а также проверку состояния и герметичности трубопроводов тормозной системы, эффективность тормозов, свободный и рабочий ход педали тормоза и рычага стояночного тормоза. Кроме этого при первом техническом обслуживании проверяют уровень тормозной жидкости в главном цилиндре и при необходимости доливают ее, состояние тормозного крана, состояние механических сочленений педали, а также состояние рычагов и других деталей привода. При втором техническом обслуживании выполняют работы, предусмотренные первым техническим обслуживанием, ежедневным осмотром, а также выполняют дополнительную проверку состояния тормозных механизмов колес при их полной разблокировке, заменяют изношенные детали (тормозные барабаны, колодки), а также регулируют тормозные механизмы. Кроме того, при прохождении второго технического обслуживании прокачивают гидропривод тормозов, проверяют работу компрессора, а также регулируют натяжение приводного ремня и привод стояночного тормоза. Сезонное обслуживание автомобиля и его тормозной системы, как правило, совмещают с работами, выполняемыми при втором техническом обслуживании, а также производят работы в зависимости от сезона. Работы по регулировке тормозной системы включают в себя устранение подтекания жидкости из гидропривода тормозов и его прокачку от попавшего воздуха, регулирование свободного хода педали тормоза и зазора между колодками и барабаном, а также регулировку стояночного тормоза. Подтекание тормозной жидкости из тормозной системы устраняется подтягиванием резьбовых соединений трубопроводов. В том случае, если причина подтекания — в неисправных деталях, то эти детали необходимо заменить на новые. Воздух из гидропривода тормозной системы автомобиля удаляют в следующей последовательности: 1) выполняют проверку тормозной жидкости в наполнительном бачке главного тормозного цилиндра, а также при необходимости доливают ее; 2) снимают резиновый колпачок с клапана выпуска воздуха колесного тормозного цилиндра и затем на него надевают специальный резиновый шланг, другой конец которого опускают в емкость с тормозной жидкостью; 3) отворачивают клапан выпуска воздуха на полоборота и резко несколько раз нажимают на педаль тормоза; 4) удерживают педаль тормоза в нажатом положении до полного выхода воздуха из системы торможения; 5) закрывают клапан при нажатой тормозной педали. После этого осуществляют подкачку остальных колесных цилиндров в том же порядке..В процессе прокачки необходимо постоянно добавлять тормозную жидкость в наполнительный бак. После прокачки педаль торможения станет более жесткой, ход педали восстановится и будет в пределах допустимого. На большинстве легковых автомобилей регулировка зазора между колодками и тормозным барабаном осуществляется автоматически. При изнашивании тормозных колодок происходит перемещение упорных колец в колесных тормозных цилиндрах, в результате чего происходит регулировка зазора между колодками и тормозным барабаном. На автомобилях, не оснащенных автоматической регулировкой, зазор регулируют при помощи поворота эксцентрика. В автомобилях с пневматическим приводом системы торможения регулировка зазора осуществляется при помощи регулировочного червяка, который устанавливается в рычаге разжимного кулака. Для регулировки зазора необходимо вывесить колесо и затем, поворачивая ключ червяка за его квадратную головку, довести колодки до контакта с барабаном. После доведения колодки необходимо поворачивать червяк в обратном направлении, до тех пор, пока колесо автомобиля не начнет свободно вращаться. Правильность регулировки зазора проверяют при помощи щупа. При правильной регулировке зазор должен составлять 0,2-0,4 мм у осей колодок, а ход штока тормозной камеры должен быть в пределах от 20 до 40 мм. Регулировка свободного хода тормозной педали в тормозных системах с гидравлическим приводом заключается в установке правильного зазора между толкателем и поршнем главного цилиндра. Зазор между толкателем и поршнем главного цилиндра регулируется изменением длины толкателя. Длина толкателя должна быть такой, чтобы зазор между ним и поршнем составлял 1,5-2,0 мм, такая величина зазора соответствует свободному ходу педали тормоза 8-4 мм. В тормозных системах с пневматическим приводом свободный ход педали регулируют изменением длины тяги, которая соединяет педаль тормоза с промежуточным рычагом привода тормозного крана. После регулировки свободный ход педали должен составлять 14-22 мм. Рабочее давление в пневматической тормозной системе должно регулироваться автоматически и составлять 0,6-0,75 МПа. Привод стояночной тормозной системы регулируется за счет изменения длины наконечника уравнителя длины троса, который связан с рычагом. Ход рычага отрегулированного привода стояночной системы торможения должен составлять 3-4 щелчка запирающего устройства. На грузовых автомобилях регулировка стояночной системы торможения осуществляется за счет изменения длины тяги. Длину тяги изменяют, отвертывая или завертывая регулировочную вилку. В отрегулированной тормозной системе в затянутом состоянии рычаг должен перемещаться не более чем на половину зубчатого сектора запирающего устройства. Если тормозная тяга укорочена до предела и при этом не обеспечивает полного затормаживания при перемещении стопорной защелки за шесть щелчков, то в этом случае необходимо перенести палец тяги, к которому присоединен верхний конец тяги, в следующее отверстие регулировочного рычага тормоза, при этом обязательно нужно надежно затянуть и зашплинтовать гайку. После этого нужно повторить регулировку длины тяги в указанном выше порядке. Основными дефектами в гидравлическом тормозном приводе являются износ накладок и барабанов, поломка возвратных пружин, срыв тормозных накладок, а также ослабление стяжной пружины или ее поломка. При ремонте тормозные механизмы снимают с автомобиля, разбирают, затем очищают от грязи и пыли, а также от остатков тормозной жидкости. Детали тормозных механизмов очищают специальным моющим раствором, затем водой, а после этого продувают сжатым воздухом. Разборку колесного тормозного механизма начинают со снятия тормозного барабана. После тормозного барабана снимают стяжные цилиндры, тормозной цилиндр. Если на рабочей поверхности имеются различные царапины или небольшие риски, то ее необходимо зачистить мелкозернистой шлифовальной бумагой. Если глубина рисок большая, то барабан растачивают. После расточки барабана необходимо заменить накладки на увеличенный размер. Кроме этого смена накладок осуществляется, если расстояние до головки заклепок буден менее 0,5 мм, или в том случае, если толщина клееных накладок будет менее 0,8 от толщины новой накладки. Клепку новой накладки осуществляют в следующем порядке, В начале новую накладку устанавливают и закрепляют на колодке при помощи струбцин. После этого со стороны колодки в накладке просверливают отверстия, которые предназначены для заклепок. Просверленные отверстия снаружи раззенковывают на глубину 3-4 мм. Клепка накладок осуществляется медными, бронзовыми или алюминиевыми заклепками. Перед тем как приклеить накладку на колонку, ее поверхность необходимо зачистить мелкой зернистой шлифовальной бумагой, а после этого обезжирить. После этого на поверхность накладки наносят два слоя клея с выдержкой в 15 минут. Сборка осуществляется в специальном приспособлении. После сборки механизм необходимо просушить в нагревательной печи при температуре 150-180 °С в течение 45 минут. Кроме вышеперечисленных неисправностей в гидравлическом тормозном приводе возникает износ рабочих поверхностей главных и колесных цилиндров, разрушение резиновых манжет, а также нарушение герметичности трубопроводов, шлангов и арматуры. Тормозные цилиндры, которые имеют небольшие риски или царапины, восстанавливают хонингованием. При значительной величине износа тормозные цилиндры необходимо расточить до ремонтного размера. После растачивания необходимо провести хонингование. К основным дефектам гидравлического усилителя тормозной системы относятся износ, царапины, риски на рабочей поверхности цилиндра и поршня, неплотное прилегание шарика к своему гнезду, смятие кромок пальцевых диафрагм, а также износ и разрушение манжет. Цилиндр гидравлического усилителя восстанавливают шлифовкой, но на глубину не более чем на 0,1 мм. Неисправный поршень меняют на новый. Изношенные резиновые уплотнения также меняют на новые. После замены всех изношенных деталей цилиндр гидравлического тормозного привода собирают. К основным дефектам пневматического тормозного привода относятся повреждения диафрагм тормозного клапана, тормозных камер, риски на клапанах и седлах клапанов, изогнутость штоков, износ втулок и отверстий под рычаги, поломка и потеря упругости пружин; износ деталей кривошипно-шатунного и клапанного механизмов компрессоров. Наиболее сильно изнашивающимися деталями компрессора являются: цилиндры, кольца, поршни, подшипники, клапаны, а также седла клапанов. Нарушение герметичности пневматического привода тормозной системы происходит- из-за износа уплотнительного устройства заднего конца коленчатого вала, а также из-за разрушения диафрагмы загрузочного устройства. После разборки пнемопривода детали уплотнительного устройства необходимо промыть в керосине, затем удалить закоксовавшееся масло и заусенцы и затем снова собрать. Диафрагма заменяется на новую. Воздушный фильтр тормозной системы необходимо разобрать, затем промыть фильтрующий элемент в керосине, а затем продуть сжатым воздухом. Перед установкой воздушный фильтр необходимо смочить в моторном масле. После сборки и ремонта компрессор тормозной системы должен пройти испытания и приработку на специальном стенде. При ремонте тормозного крана его снимают с автомобиля. Его разборку производят в тисках, контролируя состояние всех составляющих его деталей. После замены поврежденных деталей тормозной кран собирают. Отремонтированные или замененные узлы тормозной системы устанавливают на свои места, после чего выполняют регулировочные работы.
воскресенье, 28 февраля 2016 г.
31.Ремонт рулевого управления
Диагностика и ремонт системы рулевого управления![]()
Рулевое управление состоит из рулевой колонки с рулевым колесом, рулевого привода и рулевых тяг.
В целях обеспечения безопасности движения автомобиля необходимо проверять состояние рулевого управления при технических осмотрах всех видов.
Под действием ударных нагрузок, трения и других факторов техническое состояние элементов рулевого управления изменяется. Появляются люфты в сочленениях, способствующие повышенному изнашиванию деталей. Изнашивание или неправильные затяжки и регулировки приводят к увеличению силы трения в рулевом управлении, что влияет на управляемость автомобиля и безопасность движения.
Основные неисправности рулевого управления и их причины
При тугом вращении рулевого колеса основными причинами могут быть:
– деформация деталей рулевого привода;
– неправильная установка углов передних колес,
– низкое давление в шинах передних колес;
– отсутствие масла в картере рулевого механизма;
– повреждение деталей шаровых шарниров, подшипника верхней стойки опоры;
– повреждение деталей телескопической стойки подвески.
А для механизмов червячного типа:
– перетяжка регулировочной гайки оси маятникового рычага;
– нарушение зазора в зацеплении ролика с червяком.
Основными причинами увеличенного холостого хода могут быть:
– ослабление болтов рулевого механизма (для рулевых механизмов червячного типа), гаек шаровых пальцев рулевых тяг,
– увеличение зазоров в шаровых шарнирах, подшипниках ступиц передних колес.
Проверка рулевого управления
Проверку технического состояния рулевого управления производят по суммарной величине люфта и усилию, необходимому для поворота рулевого колеса. Общая величина люфтов рулевого колеса складывается из величины люфтов в подшипниках ступиц передних колес и соединениях шарнирных тяг, шкворневых тяг, элементов и рычагов рулевого управления.
Один раз в год необходимо проверять состояние рулевых тяг, их наконечников, шарниров и защитных колпачков. В проверке нуждаются все защитные чехлы рулевого механизма. Если под колпачки и чехлы проникает вода, пыль и грязь, то шаровые шарниры тяг быстро изнашиваются. Неисправность колпачка или чехла обнаруживают по утечке смазки из шарового шарнира.
Особенности технического обслуживания рулевого управления с гидроусилителем
Механизм рулевого управления с гидроусилителем отличается высокой надежностью и не требует особого технического обслуживания. Даже при отказе насоса гидравлического усилителя можно продолжать движение.
Первой причиной отказа гидравлического усилителя чаще всего является обрыв приводного ремня насоса. Признаком слабого натяжения ремня является появление отдачи (обратного толчка) на рулевом колесе. Обычно это заметнее всего при трогании автомобиля с места, когда колеса повернуты до отказа.
Рабочая жидкость является одновременно и смазочным материалом, поэтому очень важно, чтобы ее уровень не опускался ниже установленного уровня, иначе насос может выйти из строя.
При наличии гидравлического усилителя – сервосистемы необходимо периодически проверять уровень масла, он должен быть по верхней отметке. Если нужно долить масло, то эту процедуру необходимо производить медленно, так, чтобы не образовывались пузырьки воздуха.
Также периодически нужно проверять шланги на наличие утечек, истираний, ослабление креплений.
![]()
Проверка гидросистемы
Проверка происходит следующим образом:
1.Перед проверкой гидросистемы проверяется натяжение приводного ремня насоса, проверяется техническое состояние шкива и измеряется давление воздуха в шинах.
2.Между насосом и приводом подключается манометр для прокачки системы и полного удаления воздуха.
3.Двигатель запускается, температура рабочей жидкости доводится до 65–80 градусов.
4.Рулевое колесо нужно поворачивать вправо и влево до упора при работающем двигателе с частотой вращения коленчатого вала 1000 об/мин, при этом насос гидроусилителя создает давление 79–85 кгс/см2. В течение всей процедуры кран должен быть открыт во избежание повышения температуры.
Если при закрытом кране давление низкое, то это говорит о неисправности насоса, если высокое – то неисправен предохранительный клапан насоса.
После проверки гидросистемы манометр подлежит отсоединению. При необходимости доливается рабочая жидкость и удаляется воздух из системы.
Стандартные неисправности рулевого управления с гидроусилителем:
– повышенный шум при работе рулевого управления по причине разрегулировки рулевого механизма или неисправности насоса;
– затрудненное управление автомобилем , возникающее из–за неполадок гидроусилителя – ослабления ремня или низкого уровня жидкости в бачке, из–за неисправности насоса или его клапана;
– большой люфт, получающийся в случае изношенности главного и промежуточного валов рулевой колонки, повреждения рулевого механизма или его разрегулировки.
Особенностью работы по ремонту и техническому обслуживанию гидроусилителя является постоянный контроль за попаданием воздуха в систему, который может ее разрушить.
|
30.Ремонт колес и шин
ШИНОМОНТАЖ И РЕМОНТ ШИН
Какие ассоциации вызывает у вас слово шиномонтаж? Правильно, обычно это незапланированная остановка с заменой спустившего колеса или первый снег и длинная очередь из желающих поставить зимнюю резину. На самом деле ремонт шин или сезонную замену резины можно превратить в простое и необременительное мероприятие – мобильные шиномонтажные мастерские 03 Колесо уже 5 лет работают на московском рынке автоуслуг. В этой статье мы постараемся подробно рассказать о возможностях передвижных шиномонтажных комплексов, а заодно пополним ваши знания о видах повреждений автомобильной резины и способах их устранения.
УСТРОЙСТВО АВТОМОБИЛЬНОЙ РЕЗИНЫ
Любая автомобильная шина состоит из четырех основных элементов: протектора, боковой поверхности, корда и бортов. По своему устройству, или типу конструкции, шина может быть диагональной или радиальной. Все отличие заключается в способе укладки корда, который может быть расположен между боковыми поверхностями по диагонали к колее (диагональный тип) или строго перпендикулярно (радиальный тип). Радиальный тип более распространен не случайно – такие шины лучше держат форму и обеспечивают прочное сцепление колес с дорогой.
Все шины состоят из четырех основных частей – протектора, боковых поверхностей, корда и бортов. Каждый элемент выполняет определенную функцию, а особенности повреждений и ремонта некоторых мы рассмотрим ниже.
РЕМОНТ ШИН ПРИ ПОВРЕЖДЕНИИ ПРОТЕКТОРА
Протектор обращен к поверхности дороги. Он защищает корд от повреждений, при этом обеспечивая равномерное пятно контакта с дорогой. Повреждения этого элемента встречаются чаще всего, но устранение проколов протектора обычно не вызывает сложностей. Ситуация усложняется при возникновении порезов, это требует от мастера определенной квалификации и оборудования.
Выполнять работы по устранению проколов или порезов протекторов шин можно как в обычных стационарных, так и подвижных шиномонтажных мастерских. Если размер прокола не превышает 8 мм, обычно достаточно специального жгута, который вставляется в предварительно зачищенный и обработанный прокол и вулканизируется. Если прокол имеет большие размеры, его называют порезом. Порез требует более сложного ремонта, для его устранения в шиномонтажной мастерской применяют специальные заплатки – так называемые "грибки". Шляпка такого "гибка" располагается на внутренней поверхности шины, закрывая отверстие большого диаметра.
РЕМОНТ БОКОВЫХ ПОРЕЗОВ
Боковая поверхность шины тоньше протектора, поэтому ее повреждение, особенно в условиях бездорожья, очень вероятно. Не каждый шиномонтаж возьмется за ремонт боковых порезов, но мобильные мастерские всегда имеют необходимые материалы и оборудование. Такая универсальность подвижных шиномонтажных мастерских вызвана необходимостью обеспечить возможность устранения любых повреждений – напрасный выезд не играет на руку ни репутации мастерской, ни ее рентабельности.
Ремонт боковых порезов выполняется также как и ремонт проколов протектора больших размеров. Но следует помнить, что боковой порез радиальной шины почти всегда ведет к повреждению корда, что может плачевно закончиться при некачественном ремонте. Выполнить ремонт шины на месте при боковом порезе проще, так как поиск мастерской, которая действительно качественно делает такое восстановление иногда проблематично.
ПОВРЕЖДЕНИЯ КОРДА И "ГРЫЖИ"
Корд, или каркас покрышки выполняет очень важную функцию – он необходим для сохранения жесткости и предупреждения деформаций шины при движении автомобиля и ударах колеса о неровности. Сильный удар о препятствия или выбоины на дороге может привести к разрывам нитей корда, что вызывает локальную деформацию, или "грыжу". Такое повреждение – мина замедленного действия, которую необходимо устранить как можно быстрее.
Во-первых, деформация резины приводит к разбалансировке колеса, поэтому при движении подвеска начинает испытывать нехарактерные нагрузки и раньше времени выходит из строя. Во-вторых, рано или поздно при движении "грыжа" лопается, что может привести к аварийной ситуации. Деформации такого типа требуют обязательного устранения или даже замены резины. Как правило, мобильная шиномонтажная мастерская при невозможности ремонта может доставить новую резину, поэтому быстрое решение проблемы вам гарантировано в любом случае.
ВУЛКАНИЗАЦИЯ РЕЗИНЫ
Самым высокотехнологичным и эффективным способом устранения повреждений является вулканизация резины. Его стоит применять и для боковых порезов, и для повреждений протектора, если размеры повреждения превышают 5 см. В этом случае надежность и герметичность восстановленного участка будет очень высокой. При вулканизации не используются "грибки" или заплаты, что позволяет достичь качественной балансировки после ремонта. Ремонт боковых порезов наиболее качественно можно сделать именно с помощью вулканизации.
Для выполнения работ по вулканизации необходимы специальные знания и сложное оборудование. Мобильные шиномонтажные комплексы "03 Колесо" имеют все необходимое для вулканизации на месте, а опыт работы в этом направлении превышает 5 лет.
РАВНОЕ КАЧЕСТВО, ЛУЧШИЙ СЕРВИС
Мобильные шиномонтажные мастерские 03 Колесо работают больше пяти лет. За это время они смогли доказать, что ничем не уступают традиционному сервису по ремонту колес и шин. Для современного водителя очевидны и их основные преимущества – при таком же качестве и объеме выполняемых работ клиент получает очень удобный и быстрый сервис, позволяющий экономить бесценное время.
29.Ремонт передней подвески
РЕМОНТ ЗАДНЕЙ И ПЕРЕДНЕЙ ПОДВЕСКИ АВТОМОБИЛЯ СВОИМИ РУКАМИ
Содержание статьи:
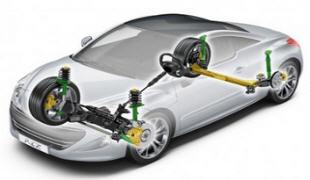
Доброго времени суток, уважаемые автомобилисты! Наступает лето, и практически прошёл весенний период интенсивного разрушения дорожного покрытия. Ям появилось больше, они видны, и все они являются «головной болью» одной из многострадальных систем – подвеска автомобиля.
Подвеска автомобиля конструктивно входя в шасси, предназначена для регулирования различных физических сил, воздействующих на авто во время движения. А состояние наших отечественных дорог делает подвеску автомобиля, наиболее подверженной к приобретению различного рода поломок и неисправностей.
С учётом того, что подвеска авто – важное звено автомобиля, как связующее его с дорогой, так и движущее его, систематическая профилактика и ремонт подвески автомобиля – святая обязанность водителя.
И вновь, мы с вами имеем право выбора: либо полностью доверится специалистам автосервиса, либо выполнить определенные операции по ремонту подвески своими руками. В первом случае мы только теряем, свои денежные знаки. Во втором, мы экономим деньги и приобретаем опыт. Выбор, как всегда, за вами.
С ЧЕГО НАЧИНАТЬ РЕМОНТ ПОДВЕСКИ АВТОМОБИЛЯ
Конечно же, это риторический вопрос. Ведь все, даже новички, вчера севшие за руль, прекрасно понимают, что ремонт автомобиля начинается с диагностики, диагностики подвески, в том числе. Не исключением является и ремонт подвески автомобиля.
Диагностика передней и задней подвески, в принципе, ничем не отличается. Кроме того, что в передней подвеске автомобиля сконцентрированы детали и узлы, которые прямым образом связаны с управлением авто. Это означает, что диагностика и ремонт передней подвески будет занимать большую часть вашего времени, чем ремонт задней подвески.
Виды диагностики подвески:
- Компьютерная – применяется лишь для авто с электронными системами управления. То есть данный вид диагностики совершенно неприменим для старых моделей.
- Вибростенд – имитирует для подвески условия, приближённые к «боевым», т.е. отечественно-дорожным. Специалисты всё чаще приходят к мнению, что диагностика на вибростенде даёт общее представление о параметрах состояния подвески, которые не имеют практической ценности. Вибростенд всегда покажет неисправность, т.к. его показатели сравнивают с заводскими параметрами.
- Ручная диагностика – это проверенно-народный способ, когда мы своими глазами видим и руками чувствуем: износ или люфт деталей подвески. Конечно же, производителями иномарок, такой вид диагностики и ремонта подвески не приветствуется. Но, специалисты, которых осталось не так уж и много, по разным стукам и «грюкам» лучше вибростенда определяют, где и какой ремонт подвески необходим.
Вот и мы прибегнем к старому, проверенному годами способу диагностики и ремонта подвески.
РЕМОНТ ПЕРЕДНЕЙ И ЗАДНЕЙ ПОДВЕСКИ
Традиционно ремонт передней подвески автомобиля происходит чаще. Это связано с наибольшей нагрузкой на элементы передней подвески во время движения, торможения. Плюс в передней подвеске находятся основные узлы управления автомобилем.
Не стоит забывать, что разные модели авто имеют разные конструктивные особенности подвески, как передней, так и задней. Поэтому, узнав общие принципы ремонта подвески, всё же лучше начинать ремонт передней подвески своего авто с Руководством по ремонту вашего авто в руках.
Важно! При определении неисправностей, производя ремонт передней или задней подвески, нужно уяснить для себя, что в 90% случаев, неисправные детали подвески следует заменять новыми. За исключением применения ремкомплектов в тем местах, где они предназначены или рекомендуются производителем.
Характерные неисправности передней подвески
- Неисправные амортизаторы – проверка состояния работоспособности амортизатора, пружин, опорных чашек, позволяет вам сделать вывод о замене амортизатора или его ремонте. Сегодняшнее положение дел всё чаще наталкивает нас на мысль, что замена амортизатораявляется более выгодной альтернативой ремонту. Помните, что амортизаторы нужно менять в паре на одной оси, аналогично замене тормозных дисков и колодок.
- Шаровые опоры, наконечники, ШРУСы – диагностика этих узлов проводится при помощи монтировки и ваших чутких пальцев – люфт определяется легко, в подвешенном состоянии автомобиля. Самым верным решением, при обнаружении люфта, является замена той или иной детали на новую. Особенно важно не пропустить треск ШРУСа или «шаровой». Вы же видели автомобили, стоящие посреди проезжей части с вывернутым колесом. Бешеные нагрузки на переднюю подвеску, не дают вам права ошибиться или экономить средства. Это ваша безопасность.
- Рычаги подвески – реже всего выходят из строя, естественно, если вы не участвуете в в ежедневных авторалли по бордюрам родного города. При обнаружении деформации рычагов подвески они должны меняться. Ни в коем случае не двигайтесь с «рихтованными» рычагами. Это приводит к нарушению развал схождения колес, со всеми вытекающими последствиями трудностей в управлении и «пожирания» резины. Замена рычагов подвески – операция парная.
- Резинотехнические и резинометаллические детали подвески при наличии деформаций и повреждений меняются на новые. Более того, при видимом дефекте, например, резинового защитного колпака (чехла, пыльника), именно с диагностики этой детали начинайте ремонт передней подвески.
КОГДА НУЖЕН РЕМОНТ ПОДВЕСКИ
По сути, признаки того, что пора провести диагностику, и скорее всего ремонт подвески, вы услышите сразу. Признаки одинаковы как для передней, так и для задней подвески. Ремонт задней подвескипринципиально не отличается от ремонта передней.
- скрип, стук в подвеске: износ резиновых втулок штанг, амортизаторов – требуется замена;
- осадка кузова авто: неисправен амортизатор либо пружина;
- перегрузка оси автомобиля – характерно для задней подвески;
- уход авто от прямолинейного движения: развал схождение передних колес, в задней подвеске смещение заднего моста из-за деформации штанг;
Естественно, все неисправности и их признаки, просто нереально перечислить. Но общее представление о том, на что стоит обращать свое внимание, проводя ремонт подвески автомобиля, нужно иметь.
28.Неисправности подвесок, ступиц колес, шин.
Неисправности подвесок, ступиц, колес и шин
Неисправности подвесок, ступиц, колес и шин имеют следующие признаки: шум и стук при движении, подтекание жидкости из амортизаторной стойки или амортизатора, повышенное раскачивание кузова автомобиля при движении по неровной дороге, крен кузова и увод автомобиля от прямолинейного движения, повышенный нагрев дисков колес, тряска автомобиля при движении, повышенное и неравномерное изнашивание шин.
Шум и стуки в подвеске при движении могут быть вызваны: ослаблением креплений деталей подвесок (амортизаторной стойки, амортизатора, стабилизатора поперечной устойчивости, растяжек, реактивных штанг, гаек крепления колес, изнашиванием или разрушением резинометаллических шарниров, резиновых подушек, втулок и буферов, повреждением подшипников ступиц колес, износом шаровых шарниров рычагов передних подвесок, неисправностью амортизаторной стойки или амортизатора, осадкой пружин, а также осадкой или поломкой рессор.
Ослабление креплений опор стоек, амортизаторов, креплений растяжек, стабилизатора поперечной устойчивости и других деталей подвесок проверяется и устраняется подтяжкой их креплений. Вышедшие из строя детали подвесок заменяют.
Подтекание жидкости из амортизаторных стоек или амортизаторов и повышенное раскачивание кузова автомобиля при движении свидетельствует о неисправности амортизаторных стоек или амортизаторов.
Крен кузова автомобиля возникает при неравномерной осадке пружин или рессор подвесок, а также при поломке листов рессор. Для устранения неисправности производится проверка осадки пружин и рессор в описанном ниже порядке и их замена. При этом для устранения крена кузова заменяют одновременно обе пружины передней подвески и (или) обе пружины или рессоры задней подвески.
Уводы автомобиля от прямолинейного движения могут вызвать нарушение углов установки колес, разрушение одной из верхних опор телескопических стоек, неодинаковая упругость пружин подвески, разное давление или разный износ шин. Устраняются данные неисправности регулировкой углов установки колес, заменой разрушенной опоры или потерявшей упругость пружины, обеспечением нормального давления в шинах, заменой изношенных шин.
Повышенный нагрев диска колеса может быть вызван перетяжкой или разрушением подшипников его ступицы, а также недостатком в ней смазки (при утечке через поврежденный сальник или несвоевременном обслуживании). При разрушении подшипников нагрев обычно сопровождается скребущими звуками. Для устранения неисправности необходимо добавить в ступицу смазку, заменить смазку в ступице, а также изношенный сальник (с частичной разборкой ступицы), отрегулировать затяжку подшипников либо заменить вышедшие из сроя подшипники (с полной разборкой ступицы). Следует иметь ввиду, что нагрев диска колеса может возникнуть также и при неисправности тормоза (при заклинивании тормозных цилиндров).
Тряска автомобиля при движении (вибрация при различной скорости) может быть вызвана деформацией дисков колес, деформацией шин, а также нарушением балансировки колес. Тряска кузова автомобиля из-за деформации колес и шин в результате ударов их о препятствия на дороге и появлении из-за этого погнутости дисков колес и разрывов нитей металлокорда шин обычно более заметна при движении на небольшой скорости (по вилянию передка или задка кузова) и при увеличении скорости переходит в менее заметную вибрацию. Нарушение балансировки колес проявляется при скорости более 70... 80 км/ч в виде вибраций кузова, которые при разбалансировке передних колес весьма ощутимы на рулевом колесе. Для устранения неисправности необходимо заменить деформированные диски колес и (или) шины и отбалансировать колеса на специальном стенде для динамической балансировки.
Повышенное и неравномерное изнашивание шин (рис. 259) может быть вызвано нарушением углов установки передних колес, большим износом шаровых и резинометаллических шарниров подвески, а также дисбалансом колес. Устранение данных неисправностей производится заменой изношенных деталей, регулировкой углов установки колес и их балансировкой.

Рис. 259. Виды износа и причины неравномерного изнашивания покрышки:
а — нормальный равномерный износ; б — повышенный износ середины протектора — эксплуатация шины с повышенным давлением воздуха; в — повышенный износ крайних дорожек без ступенек — эксплуатация шины с пониженным давлением воздуха; г — повышенный износ наружных дорожек передних колес (изображено правое колесо, вид сзади) — увеличенный угол схождения колес; д — повышенный износ внутренних дорожек передних колес (изображено правое колесо, вид сзади) — отрицательный угол схождения колес; е — повышенный износ внутренних передних колес дорожек со ступеньками между ними (изображено правое колесо, вид сзади) — отрицательный угол развала колес; ж — повышенный ступенчатый износ внутренних дорожек задних колес (изображено правое заднее колесо, вид сзади) — отрицательный угол развала задних колес (погнута задняя балка); з — местный износ в виде отдельных пятен (на любом колесе) — нарушена балансировка колес
27.Техническое обслуживание агрегатов трансмиссии
Техническое обслуживание агрегатов трансмиссии
Основные работы и приемы их выполнения при техническом обслуживании трансмиссии.
Ежедневное обслуживание.
Проверить уровень масла в гидромеханической коробке передач. Проверить при трогании с места и в движении работу сцепления, коробки передач, карданной и главной передач. Убедиться в отсутствии подтекания масла из картеров агрегатов.
Первое техническое обслуживание.
Проверить крепление картера сцепления к блоку цилиндров, состояние оттяжнои и вспомогательных пружин сцепления, уровень жидкости в главном цилиндре, свободный и полный ход педали сцепления, крепления механической или гидромеханической коробки. Через одно ТО-1 проверить правильность режимов автоматического переключения передач, работу блокировки стартера, включателя автоматической нейтрали и подтянуть все клеммовые соединения электропривода гидромеханической коробки ЛиАЗ-677. Проверить и подтянуть ослабленные болты крепления опорных пластин игольчатых подшипников, фланцев карданных валов и промежуточных опор: проверить состояние карданов.
Проверить крепление крышки и картера редуктора и отсутствие подтекания по разъемам и соединениям; смазать валик управления переключением передач и валик педали сцепления солидолом (на автобусе ЛАЗ-695).
Смазать промежуточные опоры карданных валов смазкой; игольчатые подшипники карданных шарниров — маслом ТАп-15 или ТАп-10; подшипники передней опоры гидромеханической передачи —смазкой.
Проверить уровень масла в картере заднего моста и колесной передачи и при необходимости долить масло ДП-14, ДП-11 или всесезонное ТАп-15, а в картер заднего моста ПАЗ-672 залить масло ТС-14,5 с присадкой Хлорэф-40.
Второе техническое обслуживание.
Проверить состояние и крепление пружины рычага выключения сцепления, крепление цилиндров гидропривода сцепления, состояние подшипника выключения сцепления и зазор между подшипником и рычагами выключения сцепления.
Проверить состояние и крепление крышек коробки передач, кронштейна рычага переключения передач и действие дистанционного привода переключения передач (на автобусе ЛАЗ-695Н).
Проверить регулировку механизма управления периферийными золотниками и крепление крышек подшипников. Один раз в год проверить исправность датчика контрольной лампы температуры масла в системе автоматической передачи и работу электромагнитов. Через 15 тыс. км пробега сменить масло в автоматической коробке передач. Через одно ТО-2 проверить затяжку гайки фланца ведущей конической шестерни главной передачи. Один раз в год проверить затяжку гаек опор коронных шестерен бортовых редукторов, затяжку болтов крепления чашек дифференциала, зацепление шестерен главной передачи.
Регулировка свободного хода педали сцепления автобуса ЛАЗ-695Н и Икарус-260. Свободный ход педали сцепления автобусов ЛАЗ-695Н и ЛАЗ-695М складывайся из двух зазоров. Первый зазор между толкателем и поршнем главного цилиндра, равный 0,5 мм, что соответствует свободному ходу педали 6—12 мм, и второй зазор между подшипником муфты и выжимными рычагами, который должен бьпь 3—4 мм, что соответствует свободному ходу педали 35—40 мм.
Для регулировки первого зазора необходимо снять оттяжную пружину, отсоединить щиток от рычага педали, отвернуть контргайку, удерживая ключом шток от проворачивания, и, поворачивая вилку штока, установить свободный ход педали 10 мм до упора штока в поршень главного цилиндра, затянуть контргайкой и собрать весь узел.
При эксплуатации автобуса первый зазор практически не изменяется, его регулируют только при замене деталей. Зазор же между подшипником муфты и рычагами выключения сцепления уменьшается за счет износа фрикционных накладок, что приводит к пробуксовке сцепления. Для регулировки второго, зазора необходимо: снять крышку картера сцепления; отсоединить шток и оттяжную пружину от рычага; отвернуть контргайку, удерживая гаечным ключом гайку штока о от проворачивания (который при регулировке должен быть вдвинут в цилиндр до упора); изменением длины штока отрегулировать зазор между подшипником муфты. Выключения и выжимными рычагами, который должен быть равен 3—4 мм. После этого собрать весь узел. Таким же образом регулируют свободный ход педали сцепления автобуса Икаруе-260. Величина зазора между толкателем рабочего цилиндра при снятой оттяжной пружине должна быть 4—5 мм, а свободный ход педали 20—25 мм На автобусе ПАЗ-672 свободный ход должен быть 25—30 мм.
На автобусе Икарус-260, кроме регулировки свободного хода педали сцепления, регулируют положение педали с помощью регулировочного болта предварительного сжатия сервопружины. Регулировку положения педали регулируют таким образом, чтобы расстояние между продолжением оси болта и центром оси пальца штока главного цилиндра было 5—1 мм. Предварительное натяжение сервопружины регулируют болтом таким образом, чтобы при переходе опорного пальца рычага педали через мертвую точку витки сервопружины не замыкались.
Удаление воздуха из гидропривода сцепления автобусов ЛАЗ-695, ПАЗ-672 и Икарус -260. Наличие воздуха в гидроприводе сцепления приводит к неполному выключению сцепления. Для удаления воздуха из гидропривода сцепления необходимо: заполнить бачок главного цилиндра тормозной жидкостью до уровня на 10—15 мм ниже верхней кромки бачка; снять за щитный колпачок с головки перепускного клапана рабочего цилиндра и надеть на головку резиновый шланг; погрузить свободный конец шланга в тормозную жидкость, налитую в стеклянную поллитровую банку, заполненную наполовину; создать в системе давление, резко нажав 4-5 раз с интервалом 1-2 с на педаль сцепления; удерживая педаль нажатой, отвернуть на ½-¾ оборота перепускной клапан рабочего цилиндра. Жидкость с пузырьками воздуха будет выходить в сосуд; по прекращении выхода пузырьков воздуха (пойдет чистая прозрачная жидкость завернуть перепускной клапан нить уровень жидкости до нормы, снять шланг и надеть колпачок.
Таким же образом удаляют воздух из гидропривода сцепления автобуса Икарус-260. Отличие состоит в том, что тормозную жидкость заливают в специальный бачок, соединенный трубопроводом с главным цилиндром. Для удаления воздуха установлены перепускные клапаны в главном и рабочем цилиндрах.
Регулировка дистанционного привода переключения передач. На автобусе ЛАЗ-695М и 695Н дистанционный привод коробки регулируют при помощи тяги. Для регулировки необходимо поставить рычаг в вертикальное положение и, изменяя длину тяги при помощи регулировочной вилки добиться нейтрального положения шестерен в коробке передач
Подготовка к работе и проверка исправности гидромеханической коробки передач. Проверить наличие масла маслоизмерительным стержнем, пустить двигатель, при небольшом открытии дроссельной заслонки затормозить автобус и включить рычаг контроллера в положение А, прогреть масло в поддоне до 40°С, поставить рычаг в положение Н и вновь проверить уровень масла, перевести рычаг контроллера в положение А и проверить работу гидромеханической передачи при малой частоте вращения коленчатого вала двигателя в режиме холостого хода. При 450 об/мин вала двигателя автобус не должен трогаться с места. При увеличении частоты вращения коленчатого вала двигателя трогание с места должно быть плавным. При разгоне автобуса и при среднем открытии дроссельной заслонки переключение на прямую передачу должно происходить при скорости 18—20 км/ч (ощущается по легкому толчку), а блокировка трансформатора — при скорости 28—30 км/ч. Разблокирование гидротрансформатора должно происходить при скорости 23—25 км/ч, а переход на понижающую передачу— при скорости 14-16 км/ч. При разгоне автобуса на полном открытии дроссельной заслонки включение прямой передачи должно происходить при скорости 28-30 км/ч, а блокировка гидротрансформатора-при скорости 38-42 км/ч, разблокирование гидротрансформатора – при снижении скорости 35-37 км/ч, а переход на первую передачу- при скорости 23—25 км/ч. Для заправки гидромеханической передачи применяют масло марки А для автоматических передач. Смену масла первый раз осуществляют через 1000км пробега, а последующие - через 15 тыс. км. Для слива масла необходимо: очистить поддон коробки и гидротрансформатора от грязи; установить специальный поддон под коробкой; вывернуть магнитную пробку и слить масло из поддона; через отверстие в нижней части картера поочередно вывернуть две пробки насосного колеса и слить масло из гидротрансформатора. При заправке необходимо: залить через отверстие маслоизмерительного стержня около 10 л масла, пустить двигатель и 2—3 мин поддерживать режим холостого хода. После этого при работе на частоте вращения коленчатого вала двигателя в режиме холостого хода долить до 5 л масла и подождав 1 мин, выключить двигатель и проверить уровень масла. При необходимости долить. Полная заправочная емкость равна 16 л.
Для проверки и регулировки механизма управления периферийными клапанами снять крышку переключателя периферийных золотников и отвести пальцем поводок в положение первой передачи, в сторону двигателя. Включить электромагнит Ml и проверить зазор между концом регулировочного винта и толкателем электромагнита Ml. Зазор должен быть 0,2 мм. При необходимости выполнить регулировки винтом. После этого отключить магнит первой передачи, перевести поводок для включения второй передачи и осуществить такую же проверку и регулировку, как и первой передачи. При регулировке периферийный клапан должен быть расположен напротив поводка. После регулировок законтрить регулировочные болты и закрыть крышку. Замыкание контактов выключателя автоматической нейтрали должно происходить при нажатии на педаль управления дроссельной заслонкой и перемещение ее в пределах 10—15 мм. При необходимости регулировки отпустить винты крепления выключателя, отрегулировать его включением в указанный момент и вновь закрепить.
Регулировку моментов автоматического переключения . передач осуществляют винтом на рычаге главного золотника. При ввертывании винта золотник выдвигается из гильзы. При этом переключение передач происходит при большей скорости движения автобуса. При вывертывании винта золотник вдвигается и переход на следующие передачи происходит при меньших скоростях. Значительное вывертывание винта недопустимо, так как это может привести к включению прямой передачи на стоянке или при трогании с места.
Проверка уровня и смена масла в главной передаче. Для проверки уровня масла в картерах главной и колесных передачах необходимо отвернуть контрольную пробку заливного отверстия главной передачи и контрольные пробки колесных передач. Уровень масла должен быть по нижнюю кромку каждого отверстия контрольных пробок. Для смены масла необходимо при возвращении автомобиля (автобуса) с линии отвернуть все контрольные пробки, Подготовив тару под масло, отвернуть сливную пробку главной передачи и пробки в каждой колесной передаче. После слива масла завернуть сливные пробки и залить масло через контрольные пробки колесных передач до уровня нижней кромки каждого заливного отверстия, после чего завернуть пробки.
Проверка исправности карданной передачи. Проверка крепления фланцев производиться на автобусе при расторможенном стояночном тормозном механизме и нейтральном положении рычага коробки передач. Если при покачивании фланцев-вилок карданной передачи будет обнаружено ослабление крепления фланцев, необходимо отсоединить соответствующий конец карданного вала, расшплинтовать гайку крепления фланца, а затем подтянуть ее до отказа и зашплинтовать. Все болты крепления фланцев карданного вала должны быть тщательно, затянуть до отказа. Покачивая вокруг оси карданный вал, убедиться в отсутствии люфта в подшипнике карданов.
При сборке карданного вала или при замене его на новом автомобиле необходимо стрелки, выбитые на трубе вала и на скользящей вилке совместить для предотвращения нарушения балансировки.
26.Ремонт полуосей
Ремонт полуосей подвески
Классическими признаками неисправности полуоси являются перегрев фланца элемента и прицепленного к нему диска колеса, посторонний шум при движении, невозможность передачи крутящего момента, а также утечка через сальник некоторого количества масла.
Причины поломокПричиной повышенного нагрева фланца и колесного диска часто становится разрушение подшипника, сопровождаемое неприятным скрежетом. Из этой ситуации автомеханиками найдено два выхода:замена подшипника полуоси и полная ее замена в сборе. Но стоит иметь в виду, что перегрев колеса еще может стать последствием неисправности тормоза.Причиной второго указанного симптома (необычного шума) – является износ шлицевого конца полуоси, вставленного в отверстие шестерни. Здесь можно выполнить снятие полуоси с транспортного средства и заменить ее на новое изделие. Проще всего решается проблема с утечкой масла. Главным виновником в этой ситуации «назначается» изношенный сальник, подлежащий безжалостной замене. А вот с нарушением передачи крутящего момента все намного сложнее замены сальника полуоси, так как возможно наличие невидимых дефектов на самом элементе или погрешностей в работе сцепления (пробуксовка). Для точного дифференцирования можно проверить, чем во время пробуксовки занят карданный вал. Если он вращается, значит, сломана полуось, а если остается неподвижным – виновато сцепление. В этом случае последующий алгоритм зависит от результатов диагностики. Ремонт полуосиРемонт полуоси предполагает снятие, проверку, замену подшипника и обратную установку. Чтобы снять ось, нужно отделить ее от фланца колеса, от тормозного барабана и изъять болты крепления подшипника. Это делается путем выпрессовки. Выпрессовав подшипник из отверстия, можно аккуратно достать и саму полуось. Главное здесь не нарушить кромку сальника.Далее выполняется проверка. Она заключается в измерении степени износа шлицов, люфта и легкости проворачивания подшипника. И, конечно, выполняется тщательный поверхностный осмотр всех рабочих поверхностей. Детали, подлежащие ремонту, восстанавливаются и помещаются на свои места. Все остальное заменяется, а последующая установка производится в обратном порядке. |
25.Ремонт привода передних колес
Возможные неисправности приводов передних колес, их причины и способы устранения
| |
Причина неисправности
|
Способ устранения
|
Вибрация при движении автомобиля
| |
Сильный износ наружного шарнира привода колеса
|
Замените вал привода в сборе с наружним шарниром
|
Деформация вала привода колеса
|
То же
|
Износ роликов внутреннего шарнира привода колеса
|
Замените внутренний шарнир
|
Ослабление гайки крепления ступицы
|
Затяните или замените гайку
|
Увод автомобиля в сторону
| |
Износ или повреждение обоймы внутреннего шарнира
|
Замените вал привода в сборе с наружним шарниром
|
Износ или повреждение наружного шарнира
|
То же
|
Повреждение или деформация вала привода колеса
|
Замените вал
|
Ослабление гайки крепления ступицы
|
Затяните или замените гайку
|
Вытекание смазки из шарниров
| |
Износ или разрыв защитного чехла наружного или внутреннего шарниров
|
Осмотрите шарнир, при наличии люфта замените. Замените поврежденный чехол и смазку
|
Недостаточная затяжка хомутов
|
Замените и надежно затяните хомуты
|
Повреждение сальника вала левого внутреннего шарнира
|
Замените узел подшипника левого внутреннего шарнира в сборе с сальником
|
Шум, стук со стороны переднего колеса при движении автомобиля
| |
Повреждение или деформация вала привода колеса
|
Замените вал привода в сборе с наружним шарниром
|
Биение вала привода переднего колеса
|
То же
|
Износ роликов внутреннего шарнира привода колеса
|
Замените внутренний шарнир
|
Ослабление гайки крепления ступицы
|
Затяните или замените гайку
|
Стук при поворотах автомобиля
| |
Сильный износ наружного шарнира привода колеса
|
Замените вал привода в сборе с наружним шарниром
|
Подписаться на:
Сообщения (Atom)